Die Instandhaltungskosten in Zeiten der Wirtschaftskrise optimieren
In Zeiten angespannter Wirtschaftsentwicklung ist es wichtig, die Instandhaltungskosten zu senken. Die Instandhaltungskosten dürfen jedoch nicht isoliert betrachtet werden. Sie stehen in direktem Zusammenhang zu den Produktionsausfallkosten. Die Ausfallkosten für eine komplexe Maschine betragen häufig mehr als 2.000 EUR pro Stunde. Ferner führt die zunehmende Automatisierung und Verkettung der Anlagen zu größerer Störungsanfälligkeit und somit zu höheren Ausfallkosten. Das Ziel muss daher sein, die Instandhaltungskosten unter Berücksichtigung der Anlagenverfügbarkeit zu optimieren.
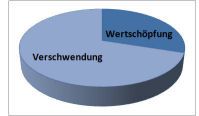
Ein Werkzeug, das sich in der Verbesserung der Produktionsprozesse bewährt hat, ist die Wertstromanalyse. Ursprünglich von Toyota entwickelt, wird anhand der Wertstromanalyse der Anteil an reiner Bearbeitungszeit von der gesamten Durchlaufzeit ermittelt. Ferner werden nicht-wertschöpfende Prozesse sowie Verschwendung, die es zu minimieren gilt, dokumentiert.
Die Wertstromanalyse lässt sich ebenfalls in der Instandhaltung einsetzen, um die Instandsetzungsprozesse zu beschreiben. Ziel dabei ist es, die Verschwendung zu minimieren.
Diverse Untersuchungen von Instandhaltungsarbeiten im Werk haben ein Verschwendungsanteil von ca. 70% ermittelt. Das Potential zur Optimierung der Instandhaltungsarbeiten ist also erheblich.
Einige Fragen, die zu beantworten sind:
- Wie lange dauert es, vom Stillstands-Beginn der Maschine bis die Betriebstechnik informiert ist?
- Wie lange dauert es für die Betriebstechnik, die richtigen Mitarbeiter und benötigten Ressourcen, wie Werkzeug und Teile, bereit zu stellen?
- Wie lange dauert die eigentliche Reparatur?
Anhand der Ergebnisse dieser und weiterer Fragen lässt sich die Verschwendung identifizieren. Der nächste und entscheidende Schritt ist die Minimierung der Verschwendungszeiten. Die Folge ist eine höhere Anlageverfügbarkeit, die mit einer Senkung der Instandhaltungskosten verbunden ist.
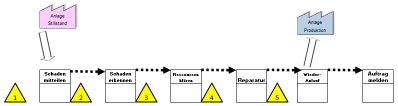