maint.tec is a powerful maintenance or CMMS software, which is available in different modules.
The main functions are:
- Preventive maintenance planning and control
- Corrective maintenance support and documentation
- Equipment documentation
- Equipment history and weak spot analysis
- Store management
- Ordering.
Extensive interfaces to equipment and ERP-systems allow for transfer of machine production time and parameter values for condition based maintenance as well as integration of maintenance, stores management and ordering in the ERP-system.
Preventive Maintenance Planning Panel
The preventive maintenance planning panel provides an overview of all tasks for the near future.
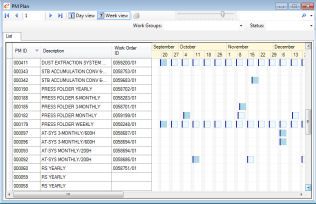
The planned tasks can be rescheduled through drag-and-drop. By double-clicking in a record one can view all the details for that task.
Preventive Maintenance Control, Parts Needed as well as Drawings, Manuals and Pictures
The maintenance tasks can be initiated either by date values or due to wear-data from the machine. Parts needed can also be defined as well as drawings, manuals and pictures related to the task.
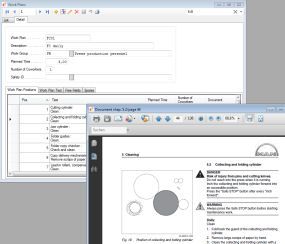
Work Order Control
Work orders can be assigned to persons and dates, when they should be carried out. Work papers can be printed and once done completed by entering reporting information.
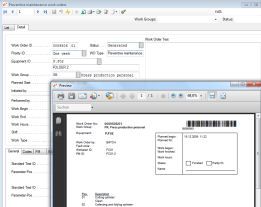
Barcodes
The work order printouts have barcodes so that they can be reported using a mobile scanner. Besides that material transactions and various readings can be registered using barcodes.
Equipment Documentation
The equipment documentation provides a central web-based administration of all manuals, spare parts catalogues and any other documents. All users have access to up-to-date information.
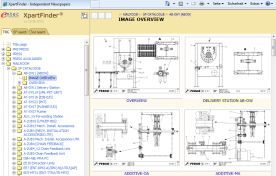
Stores Management
Based on the stores management information is available regarding spares and consumables. Which quantities are stored in which location? Powerful search functions help one quickly find needed parts.
Material Transactions
By registering the material transactions one gains transparent cost information regarding parts usage. Further the stock levels are kept up-to-date, so that needed parts can be ordered on time.
Stock Supervision
Due to stock supervision information is available concerning all parts below minimum level. Needed parts can be ordered directly from the stock supervision form.
Cost Overview
Costs are aggregated for internal work groups, external services and materials.
Budget- und Project Administration
Based on defined budgets and projects work orders, material transactions and services are related so that planned and actual costs are compared.
Personnel Capacity Planning
For each work group the available capacity is recorded. This is then related to the capacity required based on planned activities.
Visual Management
The maintenance panel provides a graphical overview of the equipment with all pending work orders and a traffic light function.
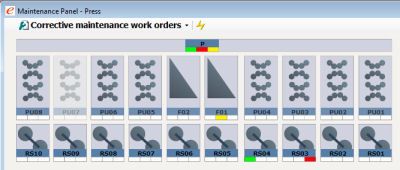
Weak Spot Analysis
Based on weak spot analysis one is able to discover damage patterns which can be circumvented either by organizational changes or in some cases changes in the equipment.
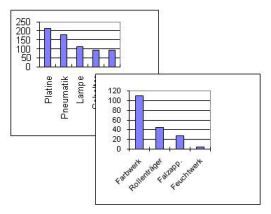
Reporting Portal
A good number of standard reports are included with maint.tec. They can be modified according to customer needs. All reports can be managed as a central web-based solution so that all users can access them.
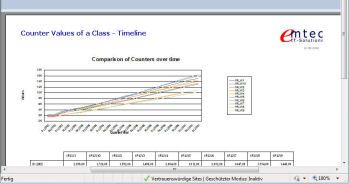
Customizing
Many parameter tables make it possible for the user to customize a number of features within the system.