Optimising Maintenance Costs in Times of Business Crisis
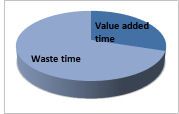
A tool which has been beneficial in improving production processes is value stream mapping. Originally developed by Toyota value stream mapping identifies the process time of the whole throughput time. At the same time non-productive processes and waste are documented, so that they can be reduced.
Value stream mapping can also be used to describe the maintenance processes. The goal is to reduce waste.
Different analyses of maintenance processes within a plant show that the portion of waste is about 70%. There is therefore a definite potential to reduce waste.
Some questions asking for an answer are:
• How long does it take until the maintenance department is informed once the machine is down?
• How long does it take for the maintenance department to inform the proper coworker and prepare all necessary resources such as tools and parts?
• How long does it take to repair the machine?
Based on these and other questions it’s possible to identify waste. The next step is to reduce the waste. The result will be higher equipment availability coupled with reduced maintenance costs.
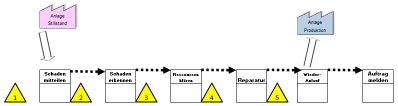