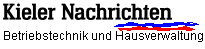
MainSys – its Practical Application in the Print Center of Kieler Nachrichten
31.05.2006
In the spring of 2003 the new print center of Kieler Nachrichten was officially commissioned. Due to a new generation of equipment in all production departments and an increased production workload it was necessary for the maintenance department to organize its processes more efficiently. We saw it as necessary to optimize the preventive and corrective maintenance as well as the spare parts management and ordering using an adequate IT-system. The previous method of handwritten repair orders using carbon copies and a self made Access program for preventive maintenance as well as a manual ordering method had to be replaced by a professional system.
In 2004 we decided to implement the MAN system MainSys. Based on an Oracle database the module “work orders” handles the preventive and corrective maintenance. The modules “stock management” and “ordering” are also widely used. Presently 15 users can work with MainSys simultaneously.
The project was implemented together with a partner of MAN, the company EMTEC. Based on our specifications a data structure was defined and the necessary data for the beginning implemented. Very soon we discovered the advantages of MainSys and were diligent to add additional data. Not only was the classical production equipment of pre-press, press and mailroom included, but we also added all equipment belonging to the facility as well as doors, stairways, rooms, etc. The diverse and steadily growing data basis simplifies our daily work tremendously.
Preventive maintenance work orders are either generated according to calendar or condition-based. Once the work orders have been completed they are reported by the management or staff members of the pre-press, press, mailroom or maintenance departments. Due to excellent search and reporting features each department has a quick overview of the status of the preventive maintenance.
Corrective maintenance work orders are mostly requested by the production departments and then taken care of and reported by the maintenance staff members, whether electricians, mechanics or technicians. Based on the reported information the one who requested the work order is kept up-to-date regarding the status of the work order and can consult with the maintenance staff if necessary.
In the daily production meeting information from MainSys is used in addition to the production reports. This gives the management an overview of the equipment condition so that repair actions as well as the time frames can be arranged by the production and maintenance management.
All preventive and corrective maintenance work orders are stored permanently in MainSys. This allows us to analyze the equipment history either using web-reports (Crystal Reports) supplied with the system or exporting data to Excel. The reports are used to find the causes for recurring faults such as web breaks or plate damages. Further they help us in tracking warranty issues, assist us in managing outsourced maintenance and compulsory inspections of equipment such as elevators, pressure tanks, etc.
In the beginning of 2005 our ordering processes were reorganized so that they were handled using MainSys. The only exception is the ordering of paper reels, which is handled using AUROSYS. Since our order volume is about 10 orders per day MainSys is more than adequate for our needs. Especially the reordering of consumables and wear parts or the ordering of spares listed in the materials module is handled efficiently. Requests for quotation are made using MainSys. We have created a report using Crystal Reports giving us a price comparison list of the quotations. Based on the RFQ it’s easy to generate a purchase order once the prices have been negotiated.
All our technical documents such as general manuals, maintenance and operation manuals, spare parts lists and drawings are stored on the server as PDF- or Excel-files and accessed via web-browser. Every user has quick access to information concerning a piece of equipment onscreen or as a printout.
Presently MainSys is used by all the departments of Kieler Nachrichten and is the most important source of information for all questions regarding corrective and preventive maintenance. Important current and past equipment information is quickly accessible for all users. The daily work has been simplified and routine work streamlined. All our purchasing processes have been optimized by the changeover to MainSys and the organizational centralizing of processes associated therewith.
Henning Hamann
Maintenance and Facility Manager at Kieler Nachrichten
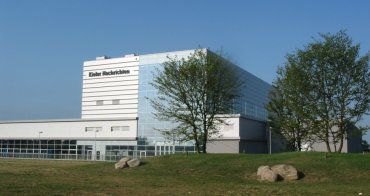
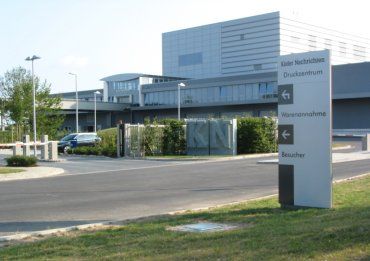
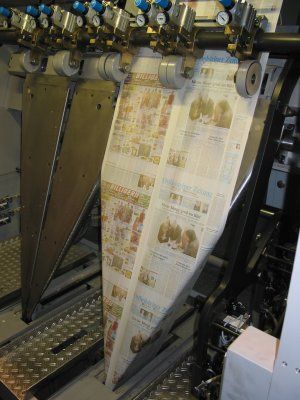
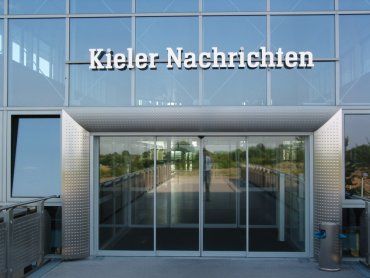